Nacht und Nebelaktion. Auf eBay einen Motor ersteigert. Lange habe ich den Onlinemarkt verfolgt um diesen einen Motor zu finden. Einen 4-Gang Simson Habicht Motor aus den 80er Jahren. Der Simson Habicht wurde nur ca. 77.000 mal gebaut. Klingt erstmal viel, aber die Wüten der DDR haben viele Exemplare verschlungen. Einen zu finden war also gar nicht so einfach. Die Motoren sind selten einzeln zu finden und wenn, dann exorbitant teuer. Aber jetzt habe ich endlich einen.
Vorgeschichte: 2015 Habe ich aus der Scheune eines alten Mühlengebäudes einen Habicht ausgegraben. Über 1,5 Jahre habe ich ihn restauriert. Alles gut, ich war super zufrieden. Der einzige Markel war, dass ein 3-Gang Schwalbenmotor verbaut war. Den hatte ich gleich mit restauriert und zum Laufen gebracht. Jetzt musste allerdings der Originalität wegen der richtige 4-Gang Motor rein, der dem Habicht damals seinen Scharm verliehen hatte. Mit den vier schön übersetzten Gängen konnte man quasi jeden Berg in solider Zweitacktdrehzahl überwinden.
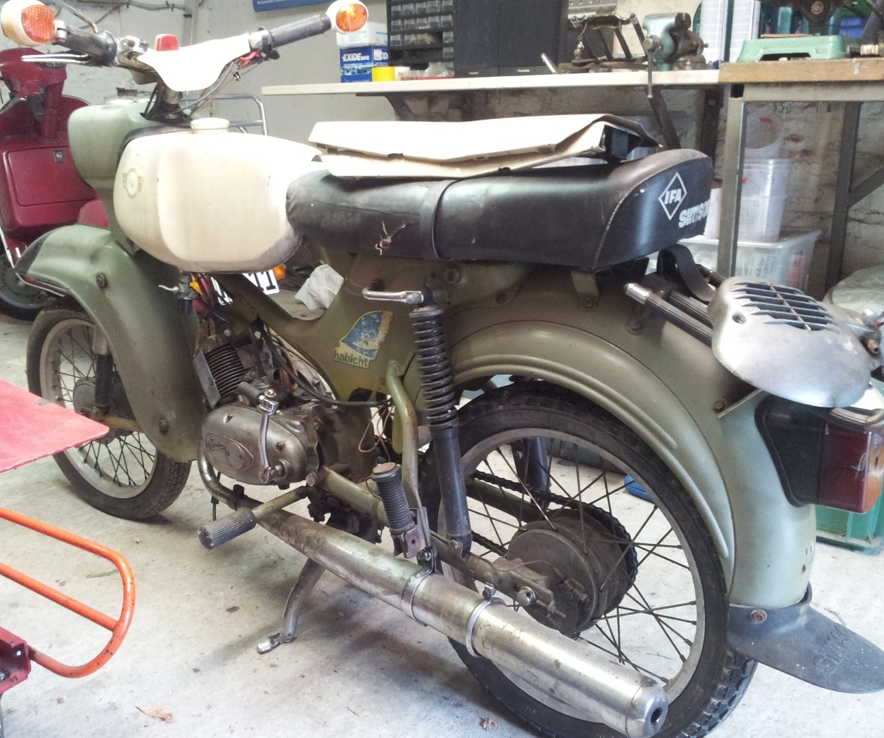
Der Dreckige Klotz
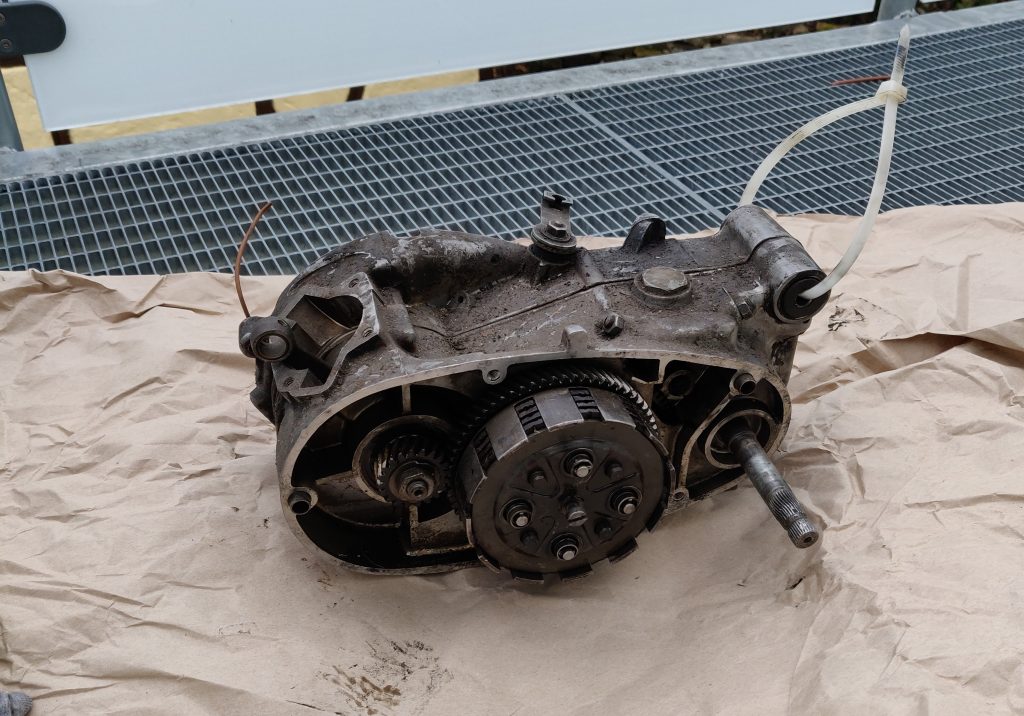
Die Basis war ein ziemlich verkommener Getriebeblock. Keine Ahnung über die Vorgeschichte. Jedenfalls drehten die Wellen noch. Ob sich die Gänge schalten ließen, wollte oder konnte der Besitzter nicht sagen. Mein Bauchgefühl sagte mir aber, dass es der richtige Kauf sei, also griff ich zu. Eine Dose Bremsenreiniger hilft gegen das zwischenzeitlich sehr fest gewordene Fett.

Von außen gesäubert, habe ich alles abgeschraubt, bis das Gehäuse auf beiden Seiten voll zu sehen war. Wellendichtringbuchsen, Kupplungskorb, Ritzel, Antriebszahnrad -Alles weg.
Demontage
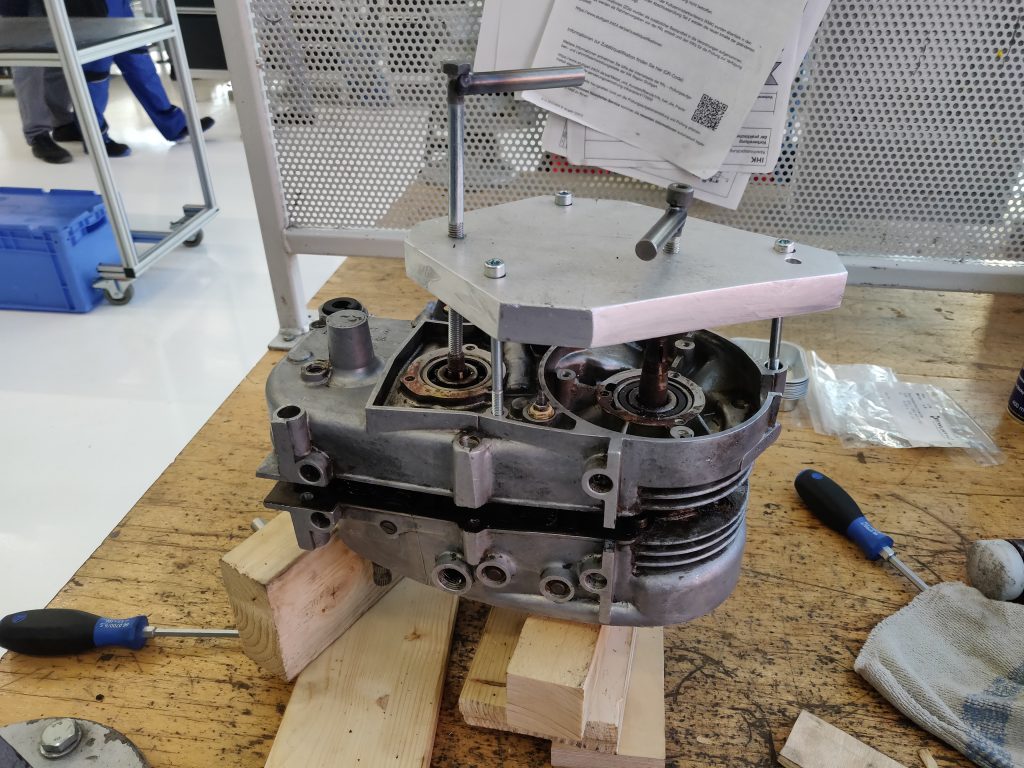
Aus einer Aluplatte habe ich mir eine Spaltvorrichtung gebaut. Wenn du die Zeichnung haben möchtest, melde dich. Mit den drei langen Schrauben in der rechten Gehäusehälfte und den zwei mittigen Schrauben auf den Dornen der Antriebs- und Kurbelwelle drückt man die Motorhälften auseinander. Damit das funktioniert, sind aus der rechten Gehäusehälfte die innenliegenden Sicherungsringe zu entnehmen. Die Wellen bleiben dann alle in der linken Gehäusehälfte stecken.
Bestandsaufnahme
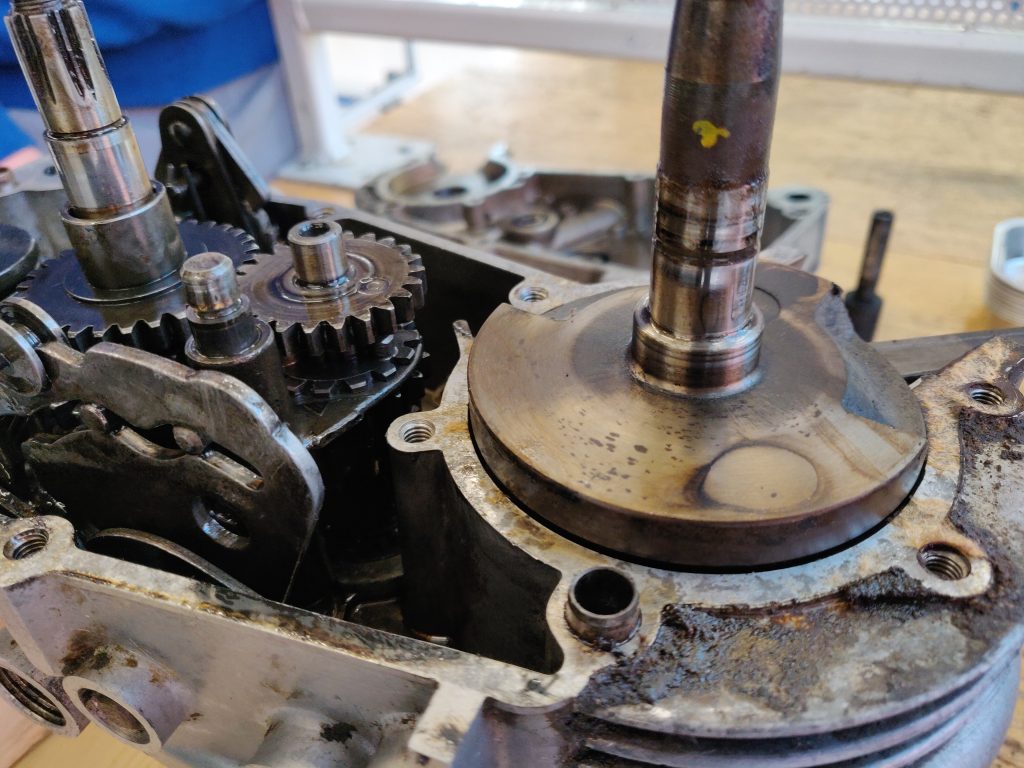
Im offenen Zustand habe ich versucht die Schaltmechanik nachzuvollziehen. Wenn man versteht, wie alles zusammen kommt, muss man nicht 1000 Fotos machen oder aufschreiben. Ich war sehr froh, dass alle Zahnräder überwiegend in gutem Zustand waren und sich die Gänge durchschalten ließen. Damit hatte ich also Glück.
Der Gehäuseschaden
Ausbruch am Stehbolzeneinsatz Ausbruch an der Bohrung für die Fußschaltung
Die linke Gehäusehälfte hatte leider zwei Ausbrüche. Anfangs war ich etwas ratlos, wie ich dieses Problem lösen sollte. Eine andere Gehäusehälfte zu verwenden hätte nicht funktioniert, da die beiden Gehäusehälften bei ihrer Fertigung miteinander verbohrt worden sind. Da hätte schon ein komplett anderes Gehäuse her gemusst. Das Gehäuse zu schweißen ist auch nicht ratsam, da der Druckguss zu schnell verläuft und seine Form verliert oder Einzelbestandteile des Gusswerkstoffes beim Schweißen verbrennen würden. Auf die Lösung brachte mich dann ein Arbeitskollege, der leidenschaftlicher Golfschrauber ist. Er hatte schon Erfahrungen mit Kaltmetall gemacht. Kaltmetall ist praktisch ein Zweikomponentenkleber. Eine metallartige Klebemasse, die sich durch einen Epoxidharz verfestigt. Man knetet es durch und nach fünf Minuten beginnt es dann auszuhärten.
Kaltmetall at it’s best: außen Masse, innen Kleber Der verklebte Ausbruch am Stehbolzeneinsatz
Damit war die erste, einfache Baustelle gefixt.
Die ausgebrochene Bohrung war ein etwas schwierigerer Fall. Dafür habe ich eine 13mm lange Alubuchse gedreht, Kaltemetall in die aufgeweitete Bohrung gesteckt und mit der Einsatzbuchse den aufgeweiteten Raum aufgefüllt (siehe Bild 1). Nach dem Aushärten habe ich die Alubuchse, an der Ständerbohrmaschine mit einem Aufbohrer, wieder ausgebohrt (siehe Bild 2). Damit war der ursprüngliche Durchmesser wieder hergestellt. An der Seite des Ausbruches habe ich den freien Platz mit Kaltmetall zur Stabilisierung verstärkt.
Bild 1: Alubuchse in der Bohrung Bild 2: nach Einkleben ausbohren
Sieht falsch aus, ist aber repariert: Bohrungsausbruch wieder heile – yes!
Le Montage
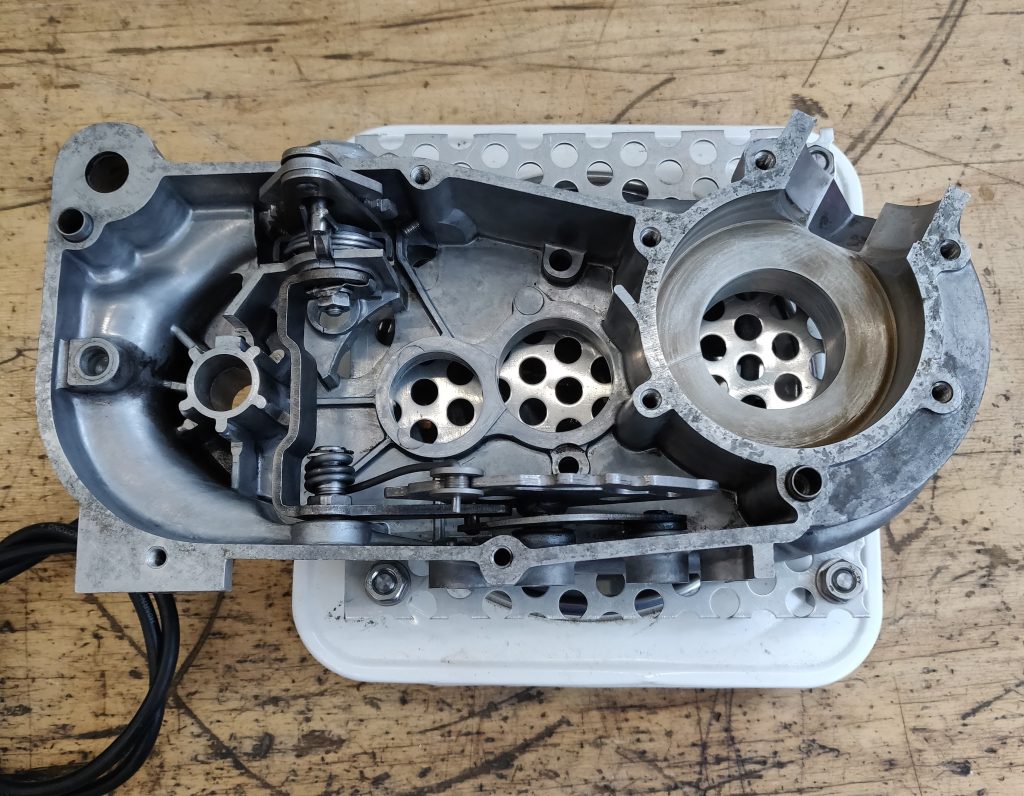
Die Lager kommen in die Tiefkühltruhe und das Gehäuse wird warm gemacht. Die Lager können dadurch in die Lagersitze reinschlüpfen. Zum Erwärmen habe ich eine Heitzsplatte verwendet.
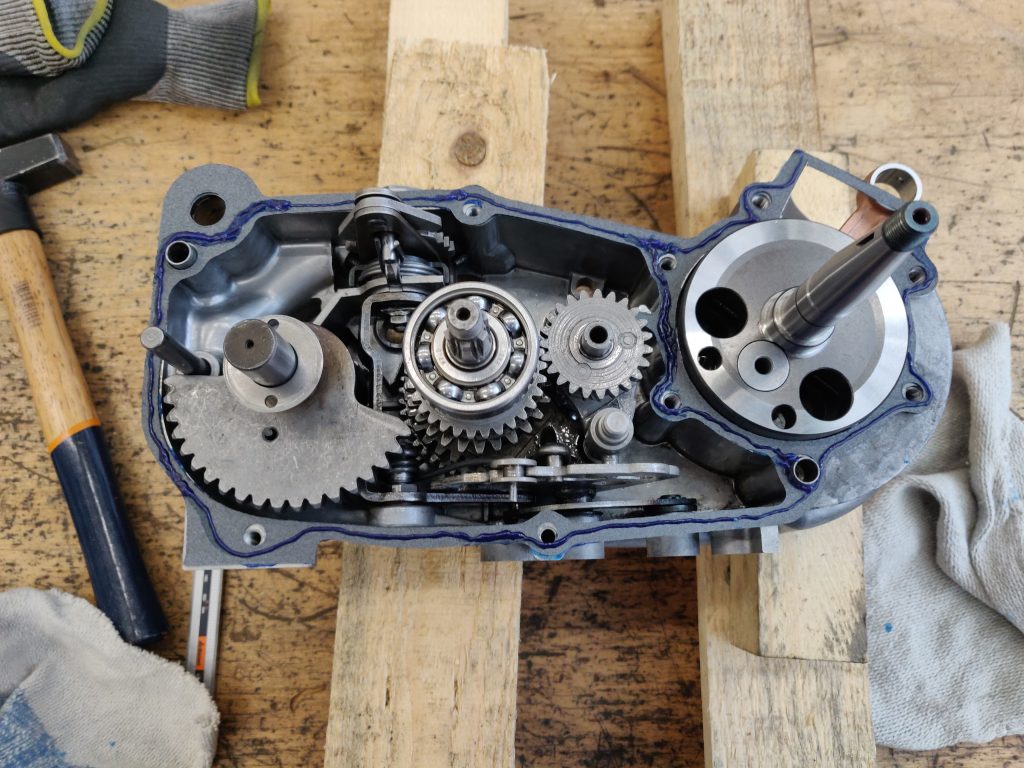
Nachdem die Lager und Wellen alle eingesetzt waren habe ich auf beide Seiten der Dichtung Dichtmasse gestrichen. Recht schnell muss man dann die beiden Gehäusehälften zusammensetzen.
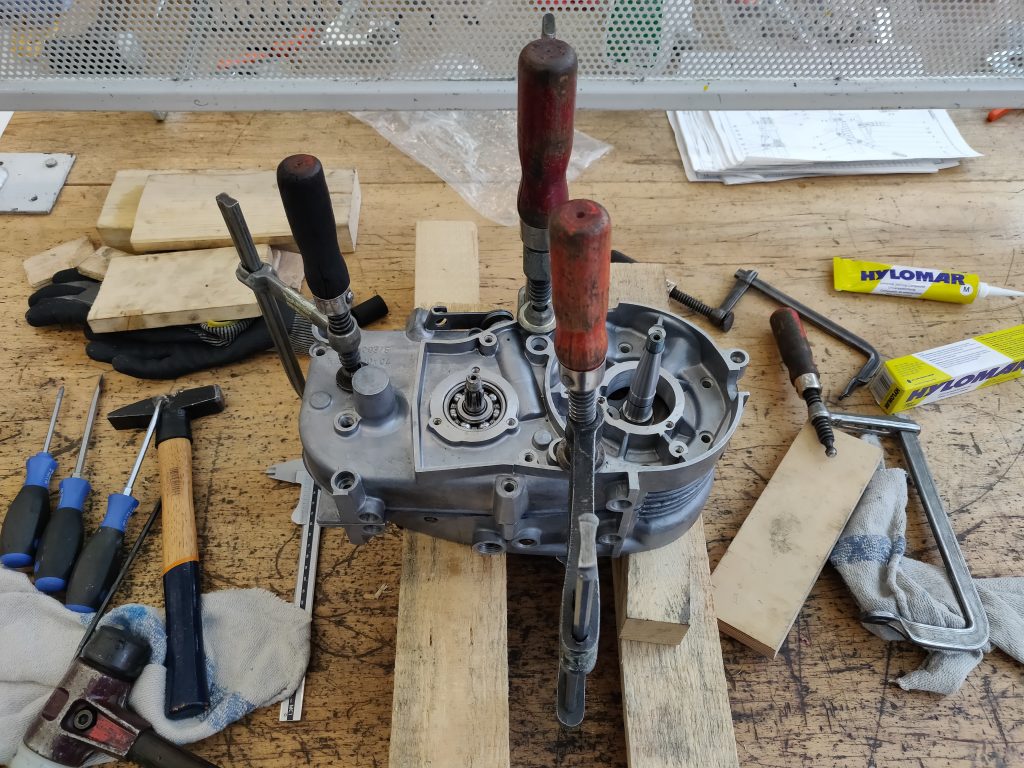
Zum aufeinander setzten habe ich einen Schonhammer und Schraubzwingen verwendet, denn dem Gehäuse muss man zur Hochzeit gut nachhelfen. Und die Dichtmasse will ja auch schnell trocken werden.
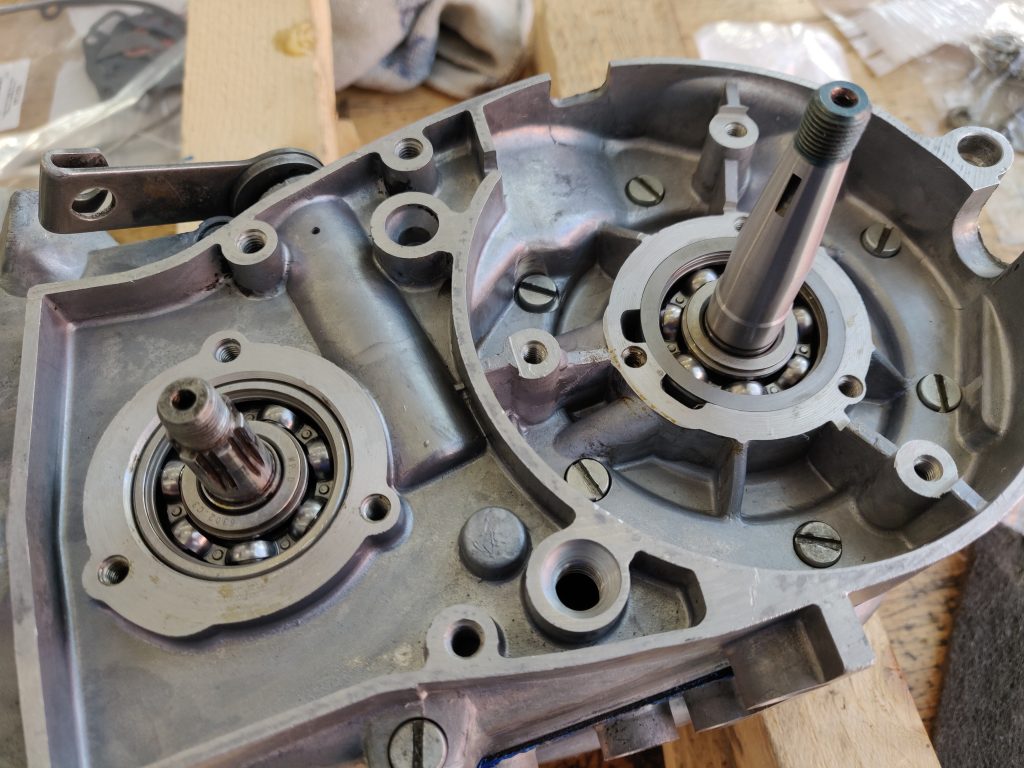
Von außen wird dann noch das letzte Kurbelwellenlager eingeschlagen. Bei der Kurbelwelle empfiehlt es sich vorher die Spalte mit einer Fühlerlehre zu checken, um dann von außen Differenzen mit Passscheiben auszugleichen. Ich habe nicht die Werte aus dem Internet eingestellt, sondern einfach gemessen mit welchen Spalten der Motor vorher gelaufen ist. Die habe ich wieder angestrebt.
Finishing Schritt für Schritt
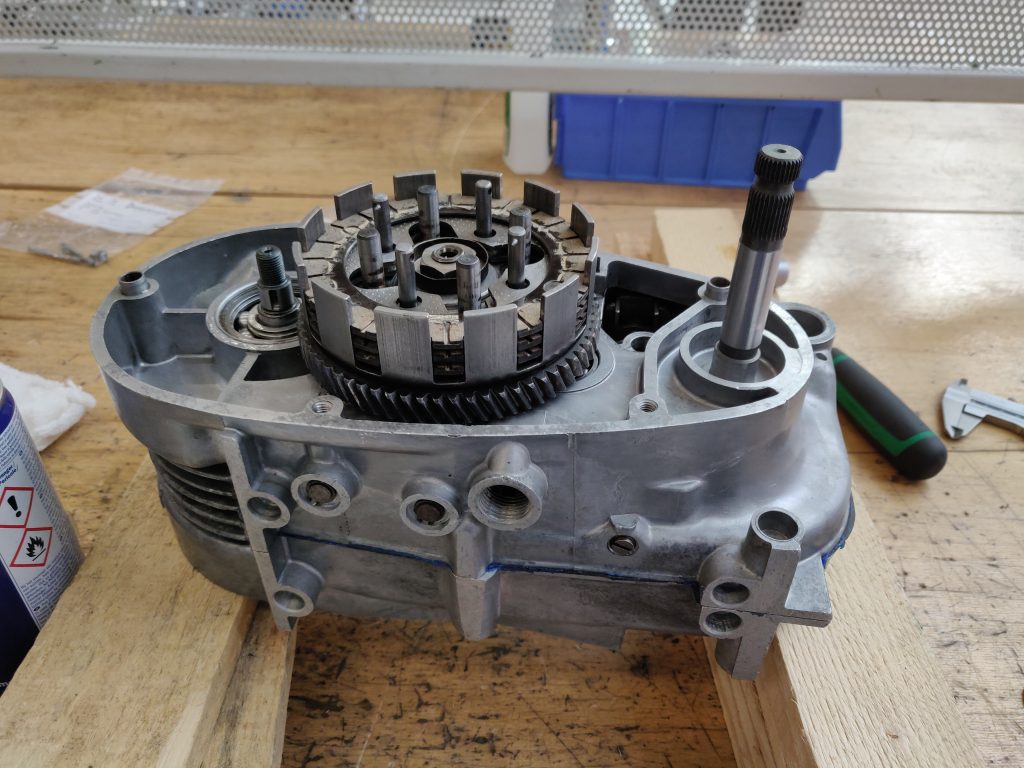
Schritt 1: Kupplung drauf.
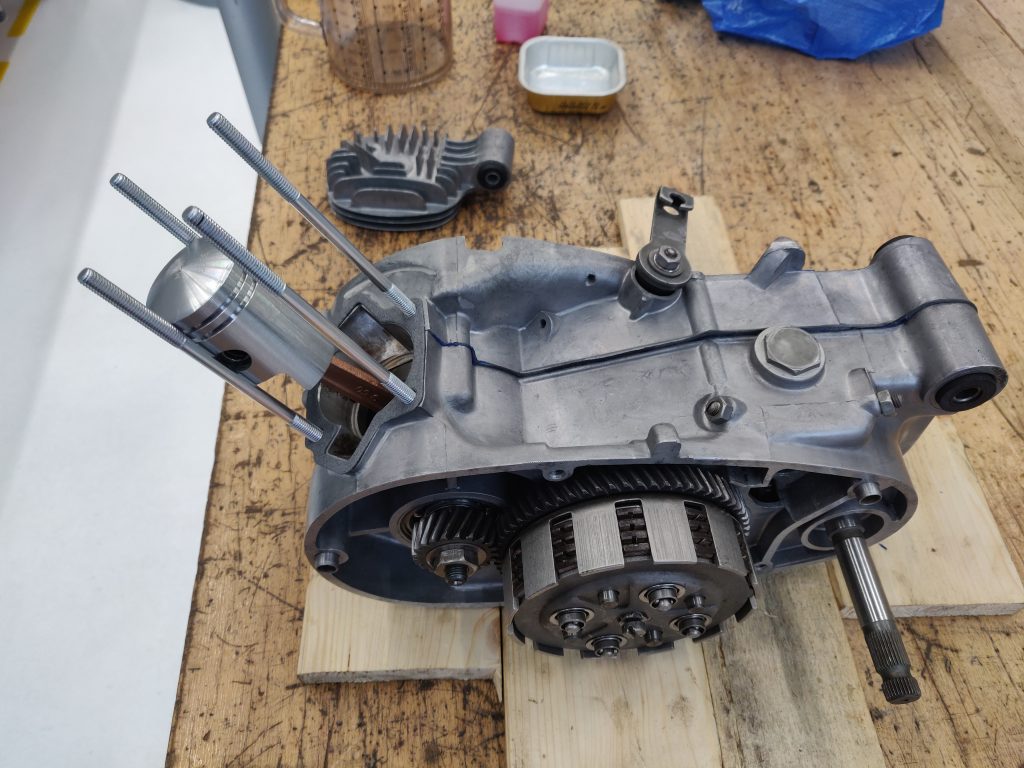
Schritt 2: Stehbolzen und Kolben mit zugehörigen Ringen anbringen.
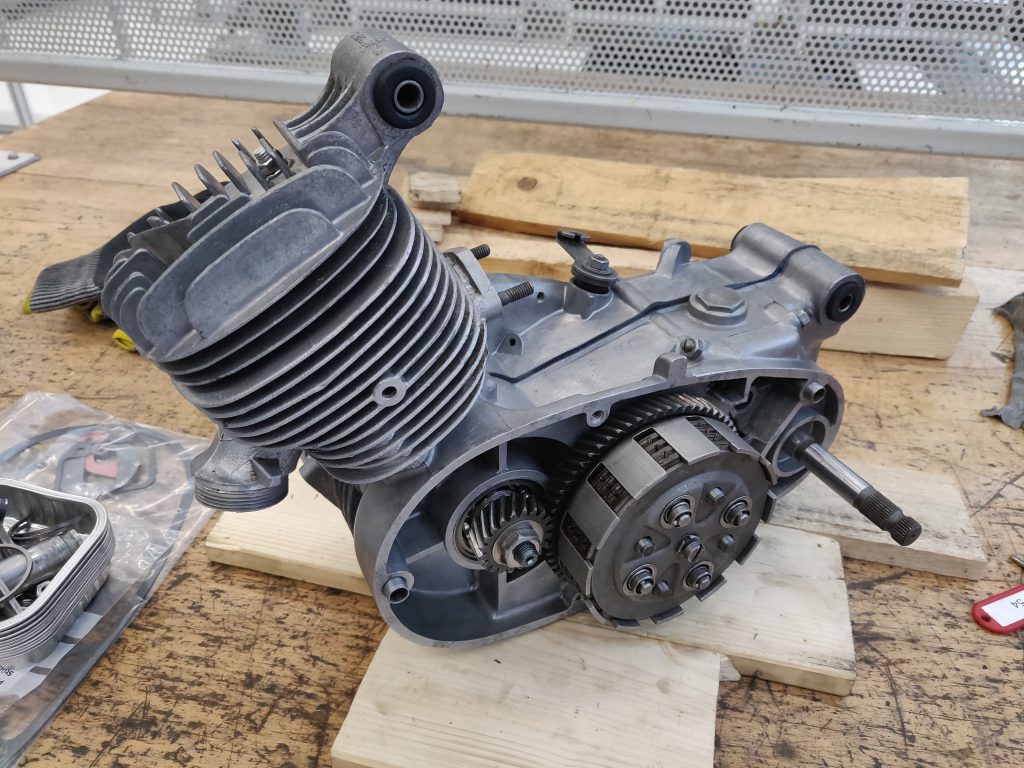
Schritt 3: Zylinder und Zylinderkopf aufschrauben.
Wozu das Ganze?
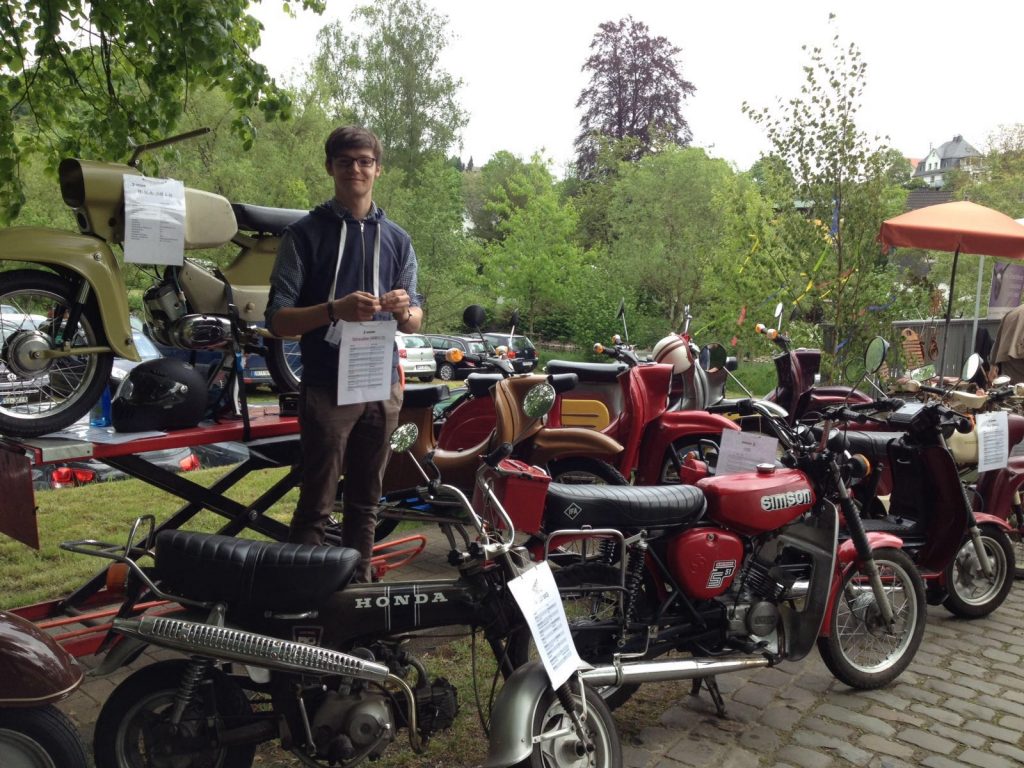
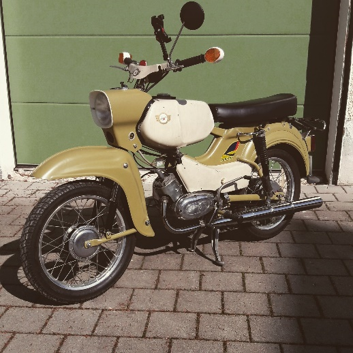
Wenn du selbst ein Simsonprojekt machst, lass doch mal austauschen!
Du studierst Maschinenbau und klebst (!!!!) dann eine belastete Stelle?
Dir ist klar, dass das nie so gut halten kann wie eine Schweißung, oder?
Das zu schweißen wäre kein großes Problem gewesen, es gibt da extra Fachpersonal für (z.B. der „Alulöffel“, einfach den Namen googeln). Ich bin selber vom studierten Fach (Materialwissenschaftler) und kann dir sagen, dass man Aluguss an sich gut schweißen kann. Es gibt auch weitere professionelle Instandsetzer, die das bestens können.
Überlege dir noch mal, ob du das nicht lieber schweißen willst.
Grüße
Lukas
Danke für dein Kommentar, ich hab jetzt auch nochmals nachgeschaut. Man kann tatsächlich Alu auf das Gehäuse aufschweißen. Mir selbst fehlt leider die Erfahrung dazu. Jedenfalls habe ich den Motor schon einige Zeit in Betrieb ohne jegliche Probleme. Ich denke meine Maßnahmen haben ganz gut funktioniert. Wenn ich ihn dann das nächste Mal zum Abdichten und Lagern wieder auseinander habe kann ich dann sehen wie empfehlenswert das Kaltmetall ist. Daraus kann man ja auch nur lernen 🙂 Grüße